Kakishibu - Persimmon Tannin Dye
- Suzanne Dekel
- Jul 25, 2022
- 5 min read
Updated: Oct 11, 2023
A blog in the series "The rarest dyes", see the blog about Murex dyeing here.
Persimmons (Latin: Diospyros kaki) are a fruit with a long history of use as food and as a dye.
Persimmon aka kaki fruit, in Hebrew אפרסמון, possumwood. These trees are usually pest-free and easy to grow in the home garden in zones 4-9.
The ripe fruits are recognizable by their typical orange color and smooth, shiny skin. Persimmons are healthy fruits (albeit with quite a bit of sugar), and an excellent source of vitamins A and C, dietary fiber, and manganese.
The Persimmon is a symbol of longevity and good luck.
Our Kakishibu powder is produced in Japan from persimmons that are grown on trees over one hundred years old. Japan produces about 300.000 tons of persimmons yearly, most of them for food purposes. Harvesting of the ripe fruits takes place during fall and early winter, a beautiful view of orange dots in a snowy landscape.

Origins of Dyeing with Persimmon Tannin
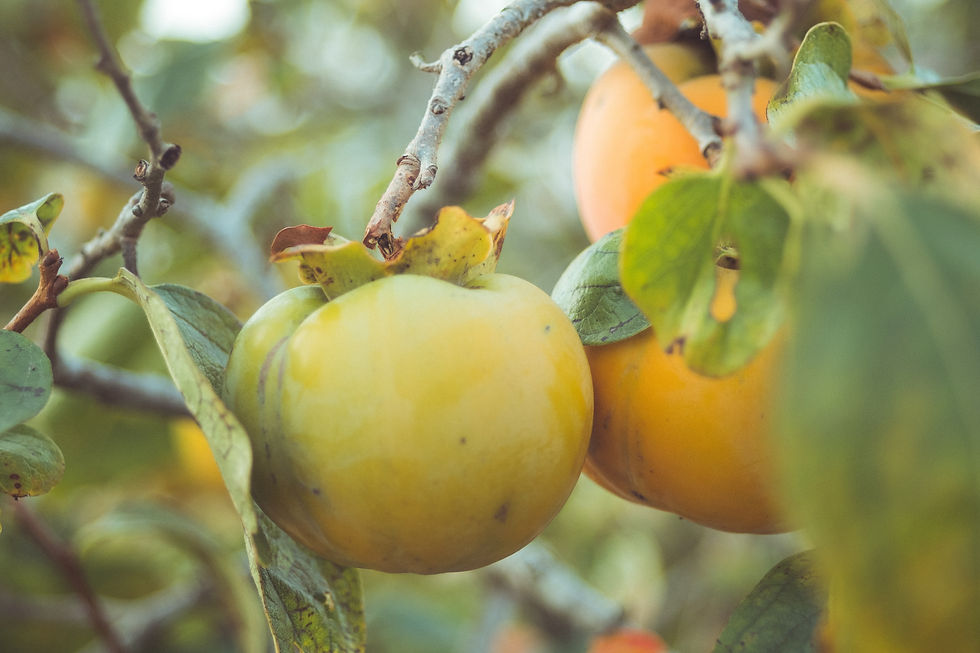
The Kakishibu dye process seems to have originated in Japan around the 13th century, 柿 KAKI is a persimmon, 渋SHIBU means astringent. The tannin-rich dye is made by crushing and fermenting unripe persimmons (Diospyros kaki L.) when they are at the height of their tannin level.
The fermentation is done by adding persimmon yeast to the persimmon pulp, then they ferment it over two years. The fermented juice can then be strained and used straight out of the container, or it can be strained, dried, and ground into a fine powder or granules. This powder should then be diluted again with plain water before use.
Traditions use persimmon as a dye.
My research shows there are similar dye traditions in Asia to the Japanese Kakishibu.
The Koreans have their Garot (갈옷): a special kind of work clothes on Jeju Island, that the Jeju people dyed with unripe persimmons, a tradition dating back to around 700 years ago.
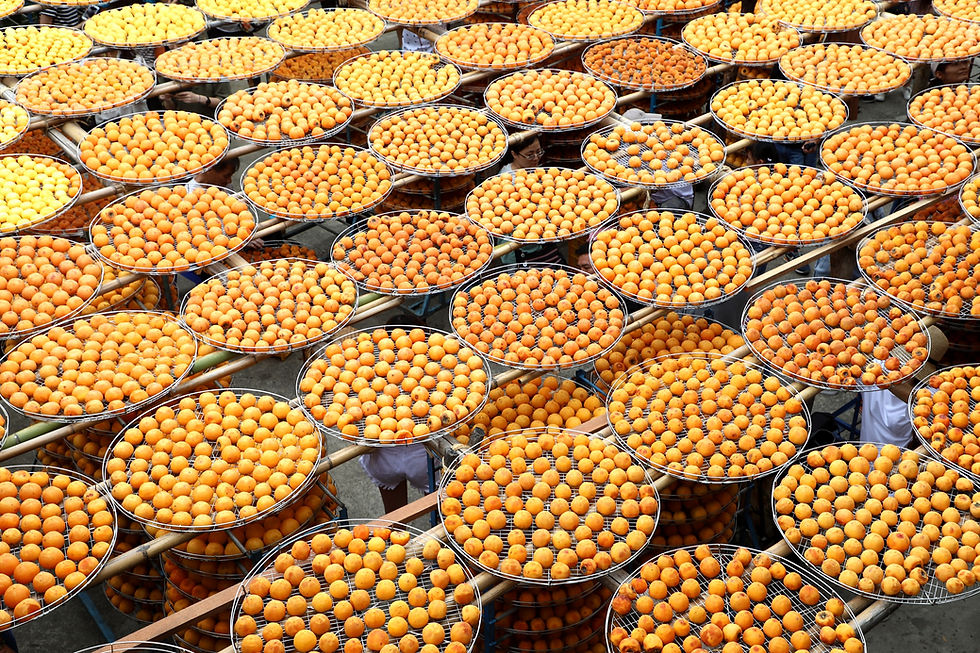
In Taiwan (客家 Hakka people) and China (Xinpu district) we can find a tradition of using persimmon dye for dyeing clothes, but here they use the peels and boil them into a thick dye. The peels are in fact a by-product of their main industry which is drying ripe persimmons on large platters in the sun to create a sweet and sticky treat you can buy online.
So what is it in Persimmons that makes it such a special dye?

The kakishibu extract we use for dyeing has a very very high tannin level (up to 95%). It is an interesting mix of condensed tannins: gallotannins, catechin, and shibuol. The latter is a tannin that is unique in unripe persimmons only.
"Fun" fact: the shibuol tannin in unripe persimmons is the reason you should never eat unripe persimmon fruits. It can cause globs to form in the digestive tract that need to be removed surgically.
When you dye with persimmon extract, the initial result will be an unimpressive yellow, coming from fugitive anthocyanidins delphinidin, malvidin, and pelargonidin in the dye. Its' final colour only develops after about a month in UV light; a lush, deep orange brown. This is why kakishibu is called an oxidative dye. Another example of a dye that turns darker in the sun is Henna.
Fabrics dyed with kakishibu are said to be water-resistant, antiseptic, insect-repellent, and mildew-proof. This would explain why it was widely used in Asia for traditional work clothes, shipping sails, and fishing lines.
Different applications.
Persimmon dye is super versatile and can be used on a variety of materials, in a variety of ways.
Making the dye:
Preparing the persimmon dye is easy: take 0.5 liter of water at room temperature and stir in 12 to 25 grams of persimmon powder (the more concentrated the solution, the darker it will be) Let this solution sit for up to 24 hours before using in a dark place, stirring regularly. Use filtered water for best results. If a bit of foamy scum forms on top of the dye, you can remove it with a paper towel. Always shake or stir the solution before use.
I use the following rule of thumb for my Kakishibu solution;
10 grams - mix with 330 ml of tepid water.
25 grams - mix with 825 ml of tepid water.
50 grams - mix with 1650 ml of tepid water.
Application on fabric:
Kakishibu is a substantive dye that does not need a mordant. You can use the Persimmon dye on cellulose and protein fibres but I find that using it on cellulose makes more sense. Cellulose has a natural affinity to tannins, and vice versa. Soak your pre-wetted, scoured fabrics for 10-30 minutes in the kakishibu dye, wring, and dry well stretched. Traditionally for Kakishibu-some, you use a wide brush and 'paint' the fabric on both sides while it is stretched between two poles..
Wearing gloves is highly recommended, the dye will stain your hands horribly.
There is no need to 'set' the dye or to heat it. Prolonged time in the dye bath will not make much of a difference.
Instead; dry your fabric in the sun, turning it every other day so the exposure will be even. You will see the fabric become darker from day to day. Because the dye is so nice and concentrated it is an excellent candidate for some creative Shibori experimenting!
After dyeing the fabric usually has a typical vinegary smell to it, but this odor evaporates in about a week.
When your fabric has fully dried and it is the hue you want, it will be a little stiff, but a quick wash in the washing machine will bring the natural softness back to the fabric

Creating other hues
For deep browns and blacks use a post mordant of 1% WOF Ferrous Sulfate. If you know me and my work you know I love to use copper sulfate, and indeed this dye gives a wonderful deep red-brown.
Coating wood:
Use a brush or sponge, and apply the dye in even strokes, going with the grain. Let the emulsion dry well before applying your next layer. Keep in mind that your final shade will be much darker than what you are initially seeing, so start with one or two layers and see if you need more after one month.
Painting paper:
Paper dyed (or painted) with kakishibu is waterproof, insect-proof, and strong. It was traditionally used as stencil paper and for making umbrellas (treated with oil to make it extra waterproof). You can make beautiful drawings with kakishibu, using it as an ink. To make ink read this blog as a guideline on how to thicken the liquid with Gom Arabic.
Making soap:
Yes, you read that correctly, and in Asia, it is a well-kept secret. Persimmon extract in soap makes it the best product for people with body odor issues, sensitive skin, or atopic dermatitis.
Storing
Kakishibu dye does not work according to WeightOfFiber, so you can just keep on using it until the last drop. For storage keep it in a tightly closed container that is properly labeled, away from children and animals, in a cool and dark place. Keeping the solution in the sun would make it oxidize which is not what we want. Before use, always shake or stir well as particles may sink to the bottom.
