Dyeing like it's 1744
- Suzanne Dekel
- 14 במרץ 2023
- זמן קריאה 4 דקות

When I was young(er) I studied classical guitar. I actually have a degree-and-a-half in it, finishing the final concert of my Masters degree but not the accompanying thesis. The topic I was assigned bored me and they wanted me to write it in Hebrew.
That made my motivation dive to historical lows until I finally just gave up altogether. But I digress.
The style I loved playing most was Baroque. It was also the style I excelled in most. I studied it in depth and did tons of research into style manners of the period. I love the music, the art, the fashion, so it will be no surprise that the dyeing practices of that period have my full interest.
In 2020 Dominique Cardon, who's work I admire much, published an in dept study of three manuscripts originally written by Antoine Janot (1700-1778). Antoine Janot was a Master Dyer from the South of France, and his manuscript 'Colors for the Enlightenment' contains rare samples and recipes of the dye practices of that time.
Tantalizing names such as 'spiny lobster', 'crow's wing' and 'sweet acacia flower' accompany the little samples of fine boiled wool that was the main export product of the South of France to the Levant.
Des Couleurs pour les Lumières gives us an unprecedented insight in the social, political and economical forces at work in the 18th century, together with scandals, great fortune and misfortune. The book is in French, and unless your French is really good it is a hard read (my high school French was not sufficient without google translate), but the true little gem is the accompanying recipe book in French and English, available here; https://www.cnrseditions.fr/auteur/dominique-cardon/
This book has been my best pastime of the entire Corona year and for a special project I have tried to rework a recipe called 'yellow wax' and I will describe step by step how I did it and what I learned from it.
This is the original wool sample of the colour I was going for, a shade called 'Yellow Wax", and next to it you see what yellow wax looks like today, used for cheese making (around the cheese, not in it).
The fabrics.
I used merino wool and merino wool jersey, wool strings and a lone piece of silk. Total of fabric; 284 grams.
Mordanting.
The first stage is mordanting; standard mordanting for all yellows with regular alum, it comes out to 16% WOF, which is only 1% more than what I usually do and recommend. A bit of cream of tartar (5.5%), which is used to keep the alum from precipitating at the bottom of the pot, and some bran. This last one was new to me, is it to absorb impurities in the water? I used regular tap water, which is of abysmal quality here in the new studio, with loads of chlorine in it according to my nose. Unfortunately this is what I have to work with until we find a better solution.
In the original the whole bolt would have been on a winch turned into the boiling bath by cheap child labour. I have neither so I left all of this with medium heat for a few hours and let it stand over night.
Dyeing.
The first stage; 80% weld (reseda luteola) (I used dried bits, I knew using my weld powder would be way too strong and taking it to green at such a percentage).
Bits, barks and roots are always best put in a bag or panty hose or mesh, whatever you can make work that is not absorbing the dye. I learned the hard way that 'saving time' by not doing this is causing irregular dye results and hours of picking the bits out of your fabric.
Heat plenty of water, add your fabrics and your bag of weld, start heating slowly and add 1% of lime (see this blog for a side by side of dyeing with, and without lime/chalk in your dye bath when using flavonoid based yellow dyes). 1.5 hours is the minimum, 3 hours is better, letting it sit overnight is best.
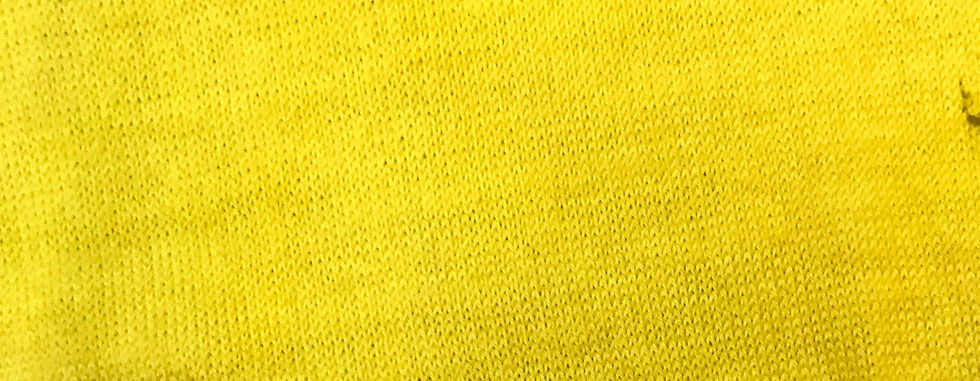
This is the shade of yellow I got on the merino jersey. A rather canary yellow.
Second stage: shading also called saddening.
Prepare a fresh bath with cold water and madder powder at 4% WOF. In the 18th century they would use what's called 'unstripped madder', the lesser quality of madder. We do not really have that distinction any more, so regular madder powder it is.
Slowly start heating the madder, and add your cooled down, reseda dyed fabrics to the pot. Now it is a matter of gauging the shade. You have to guess what your fabric will look like when it is dry, which is always 1-2 shades lighter than the wet fabric. I think I left my things in too long and it turned a bit too orange-y.

The merino jersey after shading with madder, this took the colour the most intense. A bit too dark for my taste. Amazing what 4% WOF of madder will do.

Merino wool after shading

Silk after shading, the smooth habotai part took the shading lighter than the crepe weave.

All the samples together. The new studio/storage has horrible lighting and I must invest in a better camera and lighting solution, but for now this will have to do.