I know I promised, and then things happened but after the post about logwood blue, here is the method for logwood black.

Lately I have been doing a lot of cross research, taking recipes from different (old) books such as Bancroft, Bronson and Liles and evaluating the percentages. Often this is a lot of math because some people still give recipes for a pound and then measure the mordants and dyes in ounces, so I have to 'translate' to grams and then to %WOF. Then I check what is the common factor and what is the variable between the recipes. I check two at least as is, the same way they were written out, and then I try a third batch checking if I can do the same with less...Less water, less mordant and less dye.
Because often I have been shocked at the amounts of mordants used for recipes, or the randomness of it all.
For example; J.N.Liles will say to take 1 to 2 ounces of well ground cochineal for wool, but that is double the amount...nothing to sneeze at if you want something consistent. Another example; silk mordant with alum is being recommended 8 to 16 ounces (!) of aluminium sulfate dissolved in hot water for 1 pound of silk. At 10 ounce being 285 grams that means at least 50%WOF, there is no way I personally would ever use more than 25% because of cost and wastage of minerals.
Getting a stable black can be done several ways. My teacher David Santandreux recommends indigo and madder in two steps. I tried that and it was still a bit purple. I suppose I could add yellow rustic and that would make it deeper but that experiment I will save for another day.
For the following recipe I have prepared you will need;
Cutch extract
Logwood powder
Copper II Sulfate (check if you have pentahydrate or anhydrous)
Ferrous Sulfate
Soda Ash
2 buckets and a stainless steel pot.
This recipe works for both cellulose and protein fibres.
My total weight of samples was 130 grams mixed fibres, I used silks and vintage linen.
Step 1: dissolve 10%WOFt cutch extract in hot water. stir and get rid of any lumps.
Fill a stainless steel pot with enough water to cover your textile, add textile and stir in the diluted Cutch. Do not use aluminium or this will give you a purple outcome in the final results!
Slowly heat to 60ºC, stir regularly, hold temperature for about an hour and let cool down in the pot.
There will be enough dye left for lighter shades of brown, so keep if you want to.
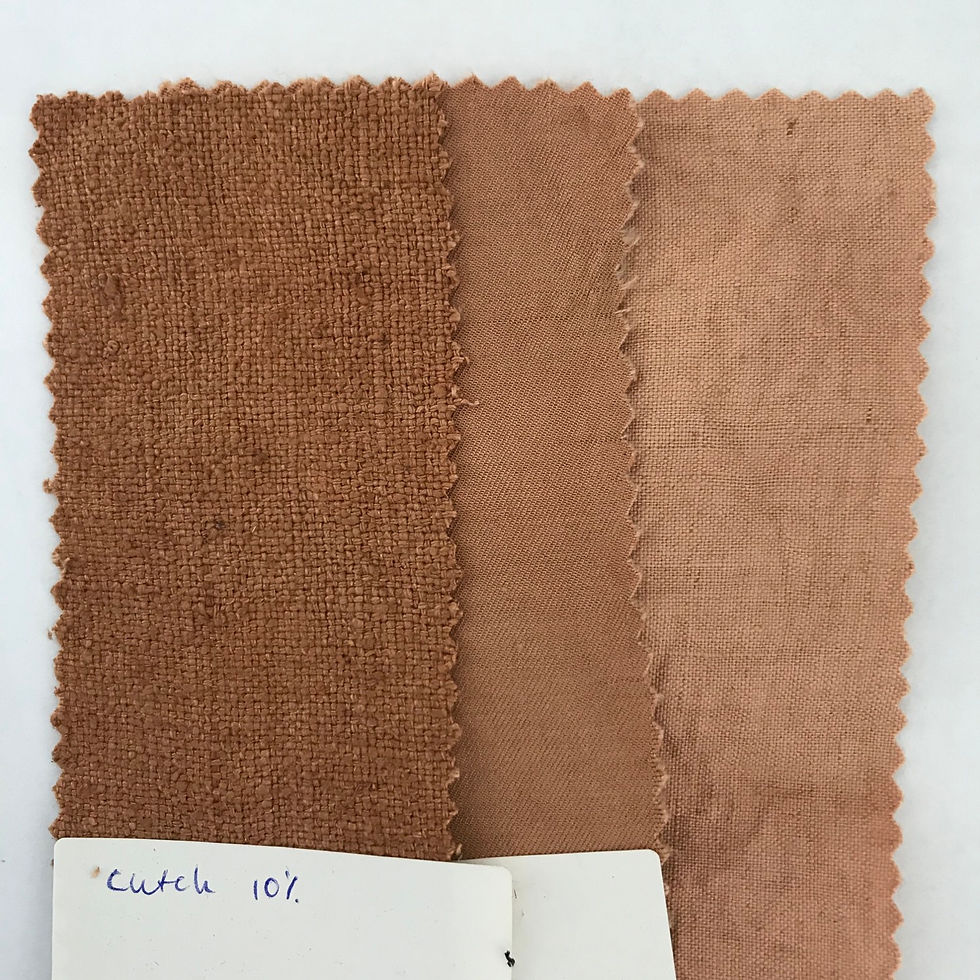
Step 2: In a bucket dissolve 1.3%WOF Ferrous Sulfate in clean, cold water.
Transfer the textile to the Ferrous Sulfate solution and work it well with gloved hands. Your textile will now turn grey. Do not feel tempted to add more ferrous Sulfate! It is bad for your hands, and bad for the textile. Do not let the fabric sit too long in this mixture, we only need it distributed even.

Step 3: In a second bucket dissolve 1% Copper II Anhydrous or 2.5% Copper II Pentahydrate. The Pentahydrate has 5 times the amount of water and is a bit more than twice as heavy as the anhydrous version.
Wring the textile from the Ferrous Sulphate water and transfer to the Copper water bucket.
Work well with gloved hands and let this sit for at least 30 minutes, even overnight is fine.
Step 4: Warm your logwood sawdust (10% WOF) in a stainless steel pan, if you use chips, put 20% WOF of the logwood chips in a pantyhose or mesh fabric. Add 10% WOF soda ash. Add the wrung textiles from the copper mordant to this dye bath and start heating the whole mixture to 60ºC for at least one hour, and let this cool down in the dye pot.

Could you do it without the Copper Sulfate?
Yes, but look at the subtle difference in hues here. Left without the copper sulfate.
It will also be less light fast.
